A fulfillment center is essential for modern businesses, handling order processing, inventory storage, picking, packing, and shipping. It boosts operational efficiency, reduces costs, and improves customer satisfaction. This guide will explore how fulfillment centers work, their benefits, and how to leverage them for business growth.
What is a Fulfillment Center?
A fulfillment center is a critical component of the supply chain, acting as a centralized hub where products are stored, orders are processed, and shipments are prepared for final delivery. Unlike traditional warehouses, a fulfillment center manages the entire order fulfillment lifecycle, including inventory management, picking, packing, and shipping operations. Its primary role is to ensure that customer orders are accurately processed and dispatched efficiently, helping businesses maintain fast delivery times and high service standards. By streamlining logistics activities, a fulfillment center enhances overall supply chain performance and supports scalable business growth.
Fulfillment Center’s Role in Supply Chains – Why is it important?
Fulfillment centers play a crucial role in modern supply chains, acting as the backbone for efficient order processing, inventory management, and logistics operations. Their importance can be highlighted through several key functions:
Order Processing and Management
Fulfillment centers streamline the order processing lifecycle, which begins with receiving customer orders and ends with delivering products to the customer. They utilize advanced order management systems to ensure that orders are processed accurately and efficiently. This includes coordinating with various departments and integrating with e-commerce platforms to automate order fulfillment, thereby reducing the time from order placement to delivery.
Inventory Storage and Management
Effective inventory storage and management are vital for maintaining optimal stock levels and ensuring product availability. Fulfillment centers are designed to store a wide range of products in organized layouts, facilitating easy access and quick retrieval. They employ inventory management systems that track stock levels in real-time, helping businesses avoid stockouts and overstock situations, which can lead to lost sales or increased carrying costs.
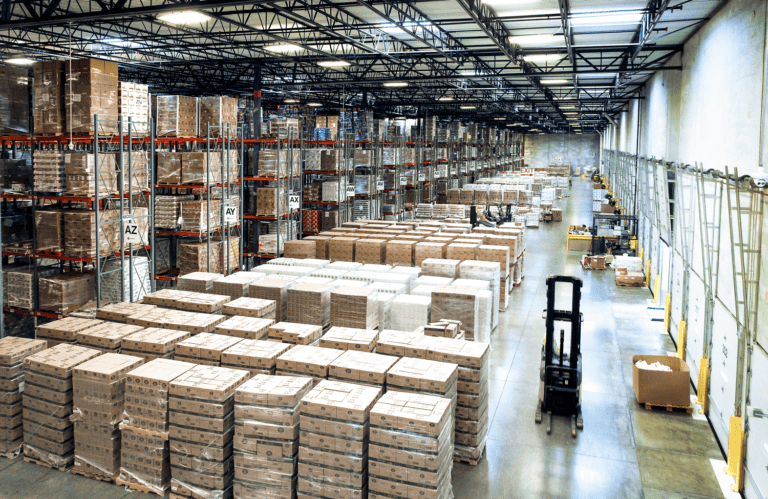
Pick and Pack Operations
The pick and pack process is a critical function within fulfillment centers, where items are selected from inventory based on customer orders and prepared for shipment. This operation can involve manual labor or automated systems, depending on the scale of the fulfillment center. Efficient pick and pack operations minimize errors and ensure that the right products are packaged correctly, which is essential for customer satisfaction.
Quality Control and Packaging
Quality control is integral to the fulfillment process, ensuring that products meet the required standards before they are shipped. Fulfillment centers implement rigorous inspection protocols to check for defects and ensure that items are in good condition. Additionally, proper packaging is crucial to protect products during transit and to enhance the unboxing experience for customers. This attention to detail helps maintain brand reputation and reduces the likelihood of returns due to damaged goods.
Shipping and Logistics
Fulfillment centers are strategically located to optimize shipping routes and reduce delivery times. They manage the logistics of transporting goods to customers, coordinating with various carriers to ensure timely and cost-effective delivery. By leveraging their relationships with shipping providers, fulfillment centers can offer competitive shipping rates and options, which is a significant advantage for businesses looking to enhance their customer service.
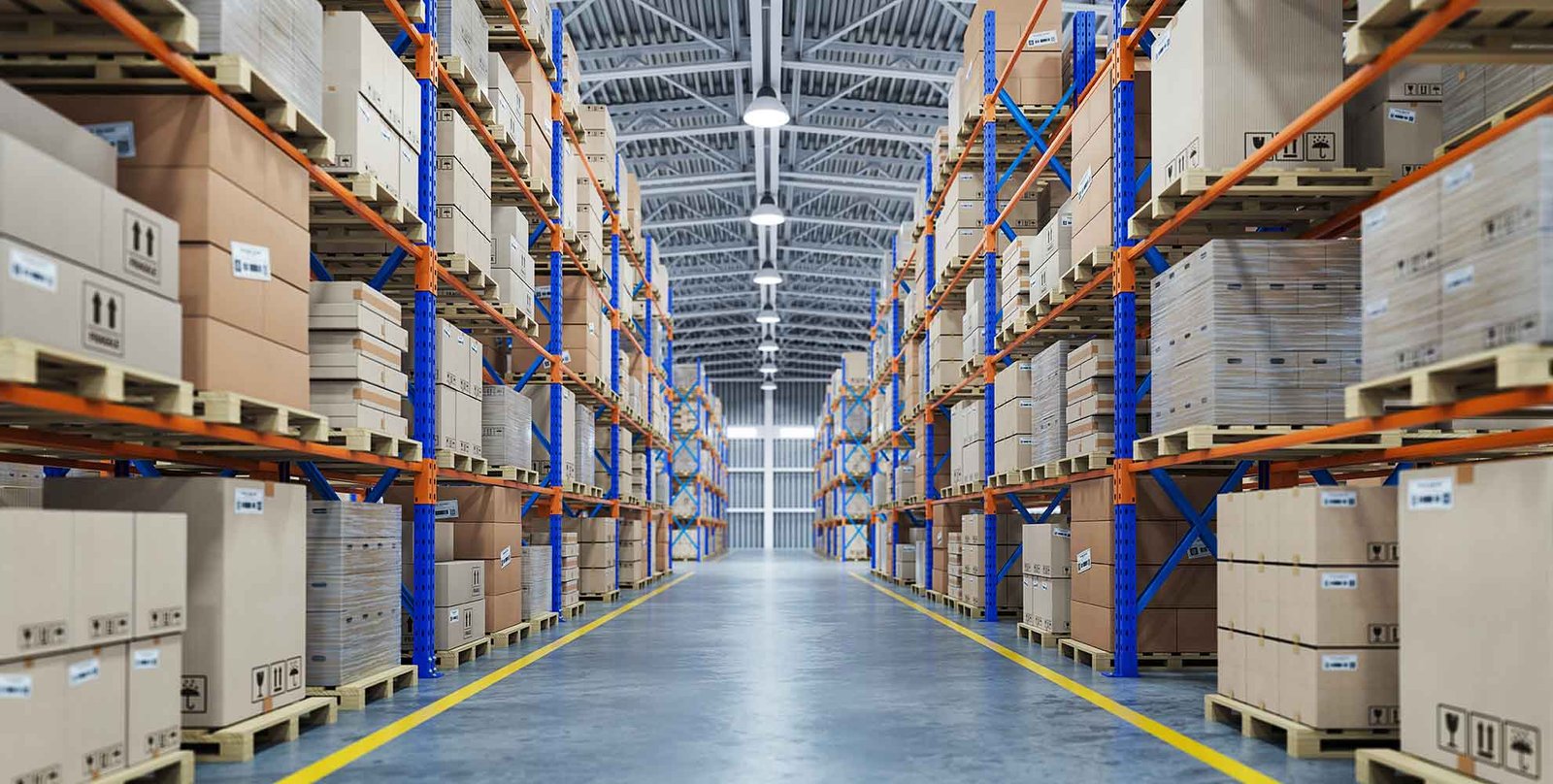
Benefits of using Fulfillment Centers
Utilizing fulfillment centers offers numerous advantages for businesses, particularly in the realm of logistics and supply chain management. Here are some key benefits:
Boost Efficiency & Accuracy
Fulfillment centers are designed to optimize the order fulfillment process, employing advanced technologies and streamlined workflows. This results in improved efficiency and accuracy in order processing, reducing the likelihood of errors during picking and packing. By automating various aspects of the fulfillment process, businesses can ensure that orders are fulfilled correctly and promptly, which is crucial for maintaining customer trust.
Speed Up Order Fulfillment
One of the primary advantages of partnering with a fulfillment center is the ability to accelerate order fulfillment. These centers are strategically located to minimize shipping times and utilize efficient logistics networks. As a result, businesses can offer faster delivery options to their customers, meeting the growing demand for quick shipping and enhancing overall customer satisfaction.
Cut Costs & Scale Smart
Fulfillment centers can significantly reduce operational costs for businesses. By leveraging economies of scale, they can negotiate better shipping rates and optimize inventory management, which lowers overhead expenses. Additionally, outsourcing fulfillment allows businesses to avoid the costs associated with maintaining their own warehousing and logistics operations. This smart scaling enables companies to allocate resources more effectively and invest in growth initiatives.

Grow with Flexibility
The flexibility offered by fulfillment centers is another critical benefit. As businesses experience fluctuations in demand, fulfillment centers can easily adjust their operations to accommodate these changes. This scalability allows companies to expand their product offerings or manage seasonal spikes in demand without the need for significant capital investment in infrastructure.
Improve Customer Satisfaction
Ultimately, the use of fulfillment centers leads to enhanced customer satisfaction. By ensuring timely deliveries, accurate order fulfillment, and efficient returns management, businesses can create a positive shopping experience for their customers. Satisfied customers are more likely to become repeat buyers and advocates for the brand, which is essential for long-term success in a competitive market.
Key Technologies and Automation in Fulfillment Centers
The integration of advanced technologies and automation in fulfillment centers is essential for enhancing operational efficiency and meeting the demands of modern supply chains. Here are some key technologies that play a pivotal role in this transformation:
Warehouse Management Systems (WMS)
Warehouse Management Systems (WMS) serve as the backbone of fulfillment operations, overseeing and managing the entire inventory and order fulfillment process. A robust WMS facilitates real-time tracking of inventory, optimizes storage allocation, and streamlines workflows by automating tasks such as order picking and shipping. By providing valuable data insights, a WMS helps businesses improve accuracy and efficiency, ultimately leading to reduced operational costs and enhanced service levels.
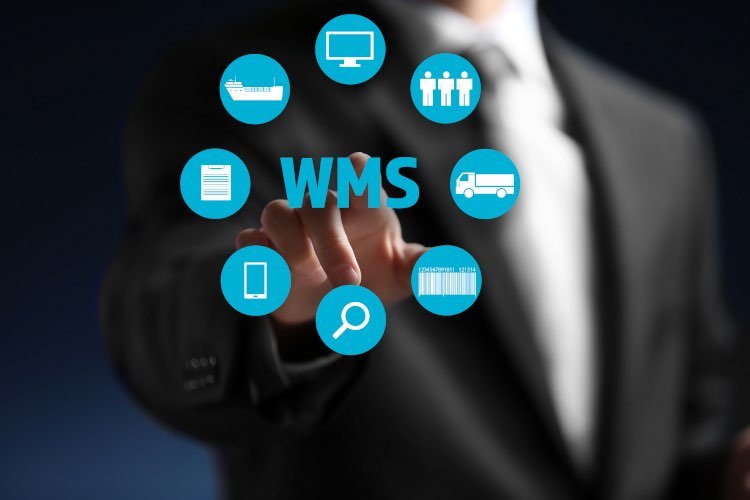
Robotics and Automation
The use of robotics and automation in fulfillment centers has revolutionized the way goods are handled. Automated systems, such as autonomous mobile robots (AMRs) and automated storage and retrieval systems (AS/RS), assist in transporting products within the warehouse, thereby minimizing human labor and increasing throughput. These technologies not only enhance speed and accuracy in order fulfillment but also allow for better space utilization within the facility.
Inventory Tracking and Management Software
Effective inventory tracking and management are critical for maintaining optimal stock levels and ensuring product availability. Inventory Management Software (IMS) provides real-time visibility into stock levels, automates reordering processes, and helps prevent inventory shrinkage. By integrating IMS with other systems, fulfillment centers can enhance their ability to respond to demand fluctuations and improve overall inventory accuracy.
Barcoding and Scanning Technology
Barcoding and scanning technologies are fundamental to modern fulfillment operations. These systems enable quick and accurate data capture during the receiving, picking, and shipping processes. By utilizing barcode scanners and RFID technology, fulfillment centers can streamline inventory management, reduce errors, and enhance the speed of order processing. This automation not only improves operational efficiency but also contributes to better customer satisfaction through timely and accurate deliveries.
Integration with eCommerce Platforms and Order Management Systems
Seamless integration between fulfillment centers and eCommerce platforms, as well as order management systems (OMS), is crucial for optimizing the order fulfillment process. This integration allows for real-time updates on inventory levels, order status, and shipping information, ensuring that businesses can respond swiftly to customer inquiries and manage orders effectively. By connecting these systems, fulfillment centers can enhance their operational agility and provide a superior customer experience.
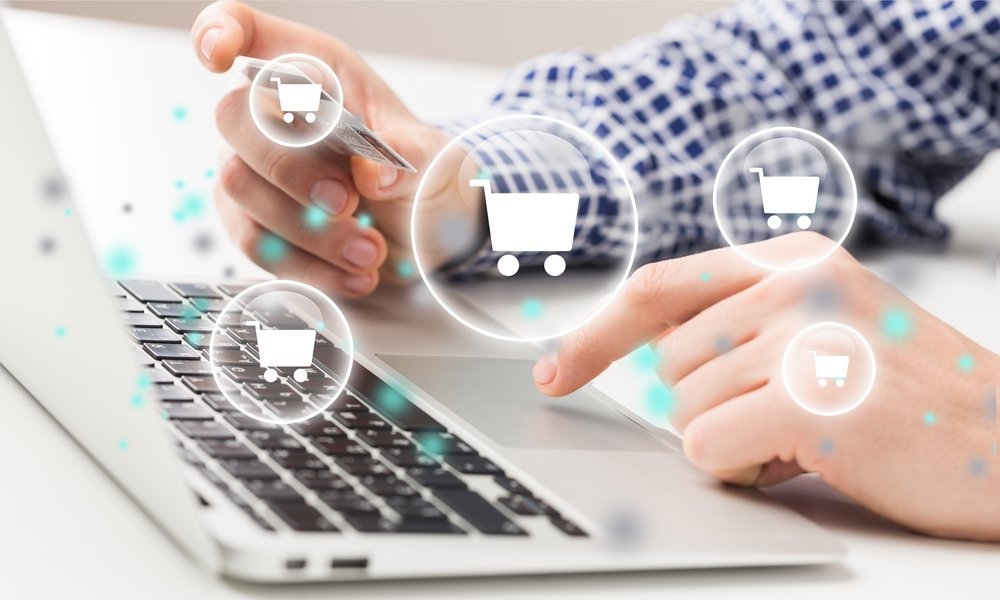
Fulfillment Center Tips for Small Business Success
Establishing an efficient fulfillment center is crucial for small businesses aiming to enhance their logistics operations and improve customer satisfaction. Here are some essential tips to consider:
Smart Warehouse Setup
A well-organized warehouse layout is fundamental to optimizing operations. Small businesses should design their fulfillment centers to facilitate smooth workflows, minimizing unnecessary movement. This includes strategically placing high-demand items closer to packing stations and utilizing vertical space for storage. Implementing a logical shelving system can also enhance accessibility and speed up the picking process.
Real-Time Inventory Tracking
Implementing real-time inventory tracking systems is vital for maintaining accurate stock levels and preventing stock outs or overstock situations. Utilizing advanced inventory management software allows businesses to monitor inventory in real-time, providing insights into stock levels and enabling timely reordering. This technology not only enhances operational efficiency but also improves customer satisfaction by ensuring product availability.
Fast Pick and Pack
Efficiency in the pick and pack process is essential for timely order fulfillment. Small businesses can adopt various picking strategies, such as batch picking or zone picking, to streamline operations. Additionally, investing in automation tools, such as barcode scanners and pick-to-light systems, can significantly reduce picking errors and speed up the packing process. This ensures that orders are fulfilled accurately and quickly, which is crucial for maintaining customer trust.
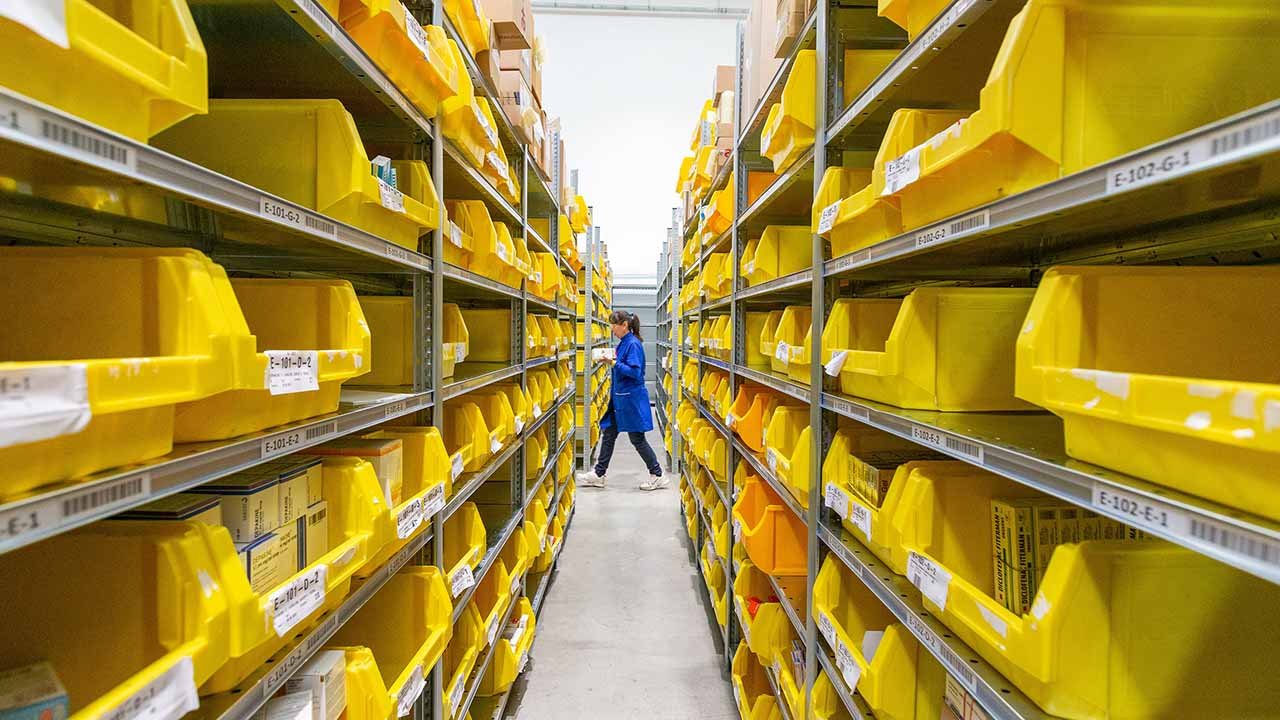
Quality Checks & Packaging
Implementing rigorous quality control measures is essential to ensure that products meet customer expectations. Small businesses should establish a systematic approach to inspecting items before they are packed, checking for defects or discrepancies. Furthermore, investing in quality packaging materials not only protects products during transit but also enhances the unboxing experience for customers. Custom packaging can reinforce brand identity and create a memorable impression.
Work Well with Shipping Partners
Building strong relationships with shipping partners is critical for optimizing logistics operations. Small businesses should evaluate various shipping options to find the most cost-effective and reliable carriers. Establishing clear communication channels with shipping partners can help streamline the shipping process and resolve any issues that may arise. Additionally, leveraging technology to integrate shipping solutions with order management systems can enhance tracking capabilities and improve overall efficiency.
Key challenges of Fulfillment Centers
Fulfillment centers play a critical role in the logistics and supply chain landscape, but they also face several key challenges that can impact their efficiency and effectiveness. Understanding these challenges is essential for businesses looking to optimize their fulfillment operations.
- Labor shortages: One of the most pressing challenges for fulfillment centers is the ongoing labor shortage. As businesses strive to meet increasing consumer demand, finding and retaining skilled workers has become increasingly difficult. This shortage can lead to operational delays and increased labor costs, ultimately affecting service levels and customer satisfaction.
- Inventory management: Efficient inventory management is crucial for fulfillment centers, yet it remains a significant challenge. Fluctuating demand, seasonal variations, and supply chain disruptions can lead to stockouts or overstock situations. Maintaining optimal inventory levels requires sophisticated forecasting and real-time tracking systems, which can be complex to implement and manage.
- Returns processing: The rise of e-commerce has led to higher return rates, which can strain fulfillment operations. Managing returns efficiently is essential to minimize costs and maintain customer satisfaction. Fulfillment centers must develop effective returns processing systems that handle inspections, restocking, and customer communication, all while keeping operational costs in check.
- Technology integration: As fulfillment centers adopt advanced technologies such as automation and artificial intelligence, integrating these systems with existing processes can be challenging. Ensuring seamless communication between various technologies, such as warehouse management systems (WMS) and inventory tracking software, is critical for optimizing operations and improving accuracy.
- Shipping and logistics coordination: Coordinating shipping and logistics is another significant challenge for fulfillment centers. With the increasing complexity of supply chains and the demand for faster delivery times, managing relationships with multiple carriers and ensuring timely shipments can be daunting. Fulfillment centers must develop robust logistics strategies to navigate these complexities effectively.
In today’s fast-moving logistics landscape, a fulfillment center plays a vital role in enhancing operational efficiency, optimizing inventory management, and delivering exceptional customer experiences. By leveraging advanced technologies and proven best practices, businesses can fully unlock the potential of fulfillment centers. Whether scaling operations or improving service speed, the right fulfillment strategy is key to success. For tailored fulfillment solutions, contact Keys Logistics today and elevate your supply chain performance.