In today’s fast-paced supply chain landscape, Inventory Accuracy plays a pivotal role in driving operational efficiency and customer satisfaction. Accurate inventory data ensures smooth order fulfillment, minimizes stock discrepancies, and reduces costly delays. As logistics networks expand, maintaining inventory precision from warehouse to last-mile delivery becomes more crucial than ever. This guide explores what inventory accuracy means, why it matters, and how to improve it across your logistics workflow.
What Is Inventory Accuracy in Logistics?
Inventory accuracy in logistics measures the consistency between recorded stock levels (in WMS/ERP) and actual physical counts in the warehouse. It quantifies how well digital records mirror physical reality. High accuracy indicates a close match, while low accuracy signals discrepancies like phantom or unrecorded inventory. Achieving 100% accuracy is challenging due to factors like human error and shrinkage.
However, striving for maximum accuracy is crucial as it provides reliable data for key operations. This data underpins accurate order fulfillment, effective demand forecasting, optimized purchasing, and trustworthy financial reporting. In the dynamic logistics environment, maintaining this digital-physical alignment is fundamental. It ensures operational integrity, efficiency, and informed decision-making across the supply chain.
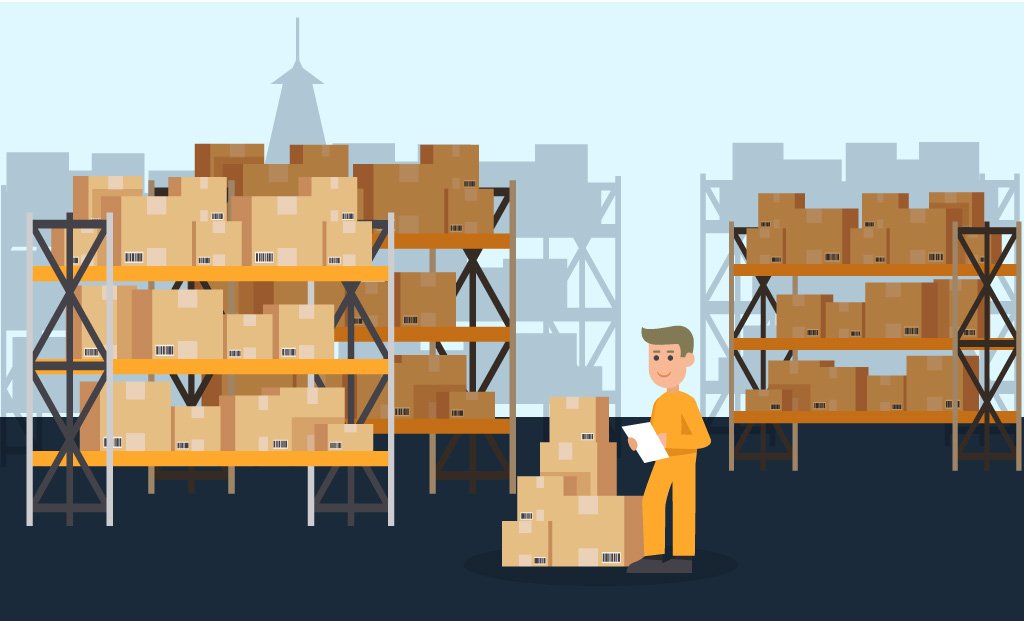
How to Calculate Inventory Accuracy
Calculating inventory accuracy provides a quantifiable measure of how well your records match reality. The most common and direct method involves comparing a physical count of items to the quantities listed in your inventory records. The standard formula is:
Inventory Accuracy Rate (%) = (Number of Items Physically Counted / Number of Items on Record) x 100
To apply this formula effectively, follow these steps:
- Define the scope: Decide whether you are calculating accuracy for a specific SKU, a particular warehouse section, or the entire inventory. For a comprehensive view, you often calculate it based on the total number of units or SKUs counted versus recorded.
- Perform a physical count: Conduct a thorough physical count of the selected inventory items. This can be done through:
- Full physical inventory: Counting every single item in the warehouse, usually done periodically. This is disruptive but comprehensive.
- Cycle counting: Regularly counting small, specific subsets of inventory on a rotating schedule (e.g., daily or weekly). This is less disruptive and allows for continuous monitoring and correction.
- Retrieve recorded data: Obtain the inventory quantity for the counted items from your inventory management system (WMS, ERP, or spreadsheet) for the exact moment the physical count was finalized.
- Compare and calculate: For each item or SKU counted, compare the physical count to the system record. You can calculate accuracy per item or aggregate the data. For an overall rate based on units: Sum the total physically counted units and divide by the total units on record for that scope, then multiply by 100.
Consistency in the counting method and timing is crucial for meaningful comparisons over time. Regular calculation allows businesses to track performance, identify trends, and measure the impact of improvement initiatives.
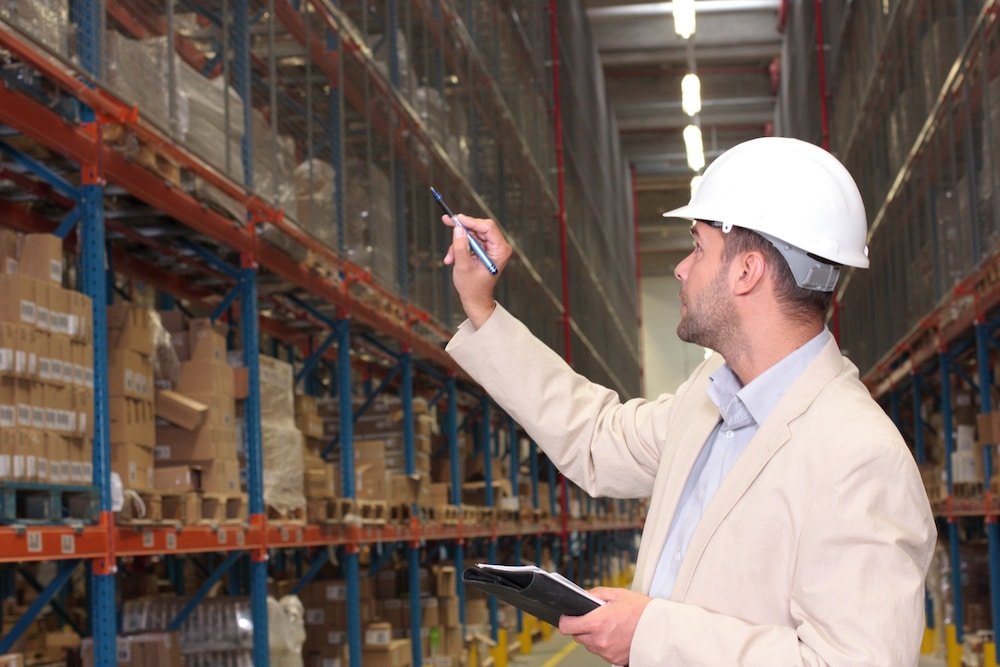
Why Is Inventory Accuracy Important?
Maintaining a high degree of inventory accuracy is not just an operational nicety; it is a strategic imperative with far-reaching implications across the entire business. Inaccurate inventory data can cripple efficiency, erode profits, and damage customer relationships. Conversely, reliable inventory data empowers businesses to operate more effectively and competitively.
Key reasons why inventory accuracy is crucial include:
- Enhanced customer satisfaction: Accurate records ensure that when a customer places an order, the product is actually available and can be shipped promptly. This prevents stockouts after orders are placed, avoids backorders, reduces fulfillment delays, and minimizes order errors, leading to a positive customer experience and fostering loyalty. Selling items you don’t physically possess is a quick way to lose customer trust.
- Reduced operational costs: Inaccuracies lead to inefficiencies. Time is wasted searching for misplaced items, performing emergency counts, or expediting shipments to correct errors. Accurate data optimizes picking routes, improves warehouse layout efficiency, and streamlines receiving and putaway processes. It also prevents overstocking (reducing holding costs like storage space, insurance, and capital tied up in inventory) and understocking (avoiding lost sales and expensive emergency orders).
- Prevention of inventory shrinkage: Accurate, real-time inventory data makes it easier to detect discrepancies caused by theft, damage, spoilage, or administrative errors quickly. Regular monitoring and reconciliation act as a deterrent to theft and allow businesses to investigate losses promptly, implementing corrective actions to minimize future shrinkage.
- Improved financial reporting and planning: Inventory is a significant asset on a company’s balance sheet. Accurate inventory counts are essential for correct asset valuation, calculating the cost of goods sold (COGS), and producing reliable financial statements. This accuracy supports better budgeting, financial forecasting, and informed investment decisions.
- Effective demand forecasting and replenishment: Reliable historical inventory data is the foundation for accurate demand forecasting. Knowing precisely what has sold and what remains allows businesses to predict future needs more effectively, optimize reorder points, and maintain appropriate safety stock levels, ensuring product availability without excessive investment.
- Optimized warehouse space utilization: Knowing exactly what inventory is on hand and where it is located allows for better organization and utilization of warehouse space. This prevents congestion, improves material flow, and can delay or eliminate the need for costly expansions.
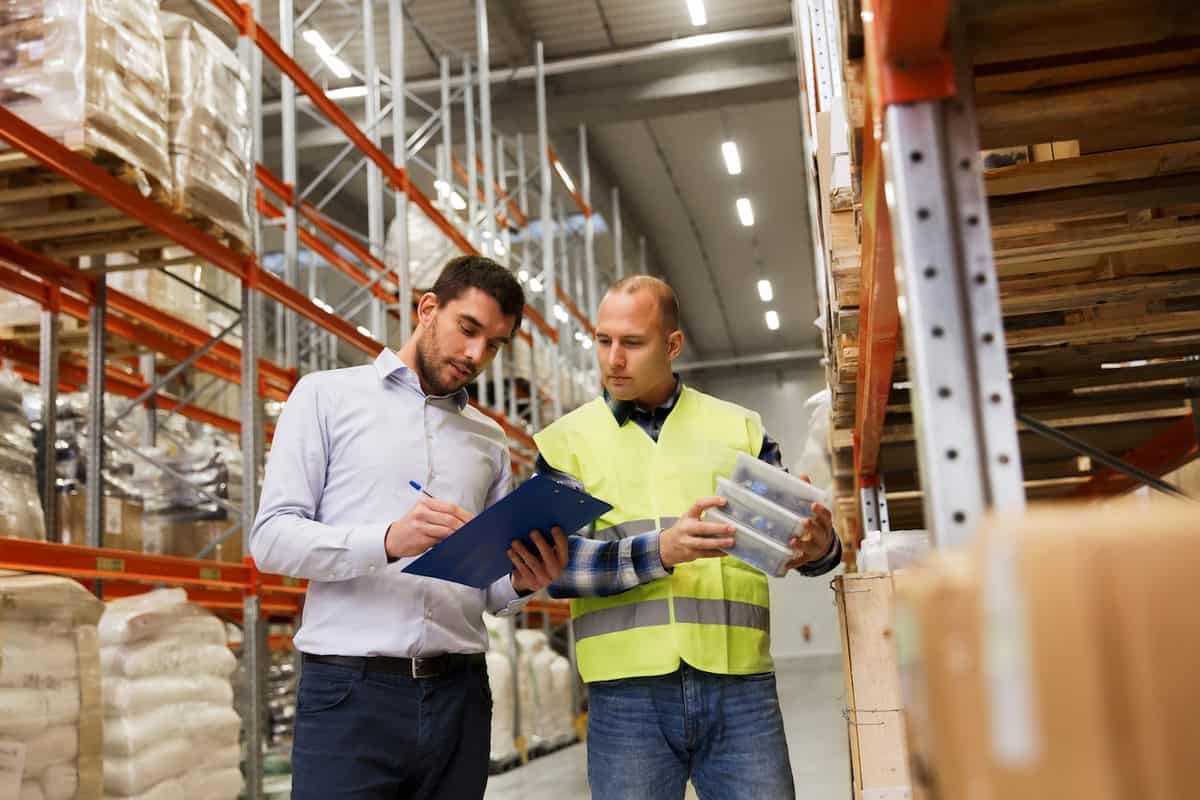
Ensuring Inventory Accuracy from Warehouse to Last-Mile Delivery
Maintaining inventory accuracy isn’t confined to the four walls of the warehouse. It extends throughout the entire fulfillment process, right up to the customer’s doorstep. Discrepancies can arise at any stage, including during transit and final delivery. Implementing technology and robust processes across this journey is key.
Using Driver Apps to Eliminate Manual Errors
Last-mile delivery often involves manual data entry or paper-based processes, which are prone to errors. Modern driver apps integrated with the central logistics system can significantly mitigate these risks. Drivers receive delivery manifests, route details, and customer information directly on their mobile devices.
Upon delivery, they can electronically confirm receipt (via signature capture, photo proof,…), scan barcodes on packages, and update the delivery status in real-time. This eliminates manual paperwork, reduces the chance of miskeyed information, confirms the correct items were delivered to the right location, and provides immediate updates back to the central system, ensuring the final step of the inventory journey is accurately recorded.
Real-Time Shipment Tracking for Transparency
Visibility during transit is crucial. Real-time tracking technologies provide continuous updates on the location and status of goods after they leave the warehouse. This transparency helps in several ways: it confirms shipments are en route as expected, allows for proactive management of delays, provides customers with accurate delivery ETAs (enhancing their experience), and helps quickly identify if a shipment goes missing or deviates from its planned route. This continuous monitoring ensures that inventory status remains accurate even when goods are outside the warehouse, reducing uncertainty and enabling faster responses to potential issues.

Data Analytics to Proactively Solve Logistics Challenges
The vast amount of data generated throughout the logistics process – from warehouse movements to final delivery confirmations – is a valuable asset. Advanced data analytics platforms can process this information to identify patterns, pinpoint recurring issues causing inaccuracies, and predict potential challenges. For instance, analytics might reveal that inaccuracies frequently occur with specific product types, during certain shifts, or on particular delivery routes.
This insight allows managers to target corrective actions effectively, such as refining processes, providing additional training, or optimizing resource allocation. Predictive analytics can also forecast potential disruptions allowing for proactive adjustments.
Optimizing Delivery Routes for Timely Fulfillment
Efficient route planning does more than save fuel and time; it also contributes to inventory accuracy in the final stages. Optimized routes ensure drivers follow the most logical sequence, reducing the likelihood of missed deliveries or packages being left on the vehicle erroneously. Route optimization software considers factors like traffic, delivery time windows, vehicle capacity, and driver schedules to create efficient and realistic plans.
When combined with driver apps and real-time tracking, it ensures that deliveries are executed as planned, minimizing deviations that could lead to discrepancies between expected and actual delivery completion, thus maintaining the integrity of the final inventory transaction record.
Tips to Improve Inventory Accuracy in Your Supply Chain
Achieving and maintaining high inventory accuracy requires a combination of disciplined processes, appropriate technology, and a culture of diligence. Here are several practical tips to enhance accuracy throughout your supply chain:
Conduct Regular Inventory Counts
Don’t rely solely on system data. Implement a schedule for physical verification. While full annual counts are often required for financial reporting, they are insufficient for operational accuracy. Supplement these with more frequent checks.
Implement Cycle Counting Programs
Cycle counting involves regularly counting small portions of inventory daily or weekly, rotating through all stock over a set period. This method is less disruptive than full counts, allows for continuous monitoring, enables rapid identification and correction of errors, and helps pinpoint root causes of inaccuracies sooner.
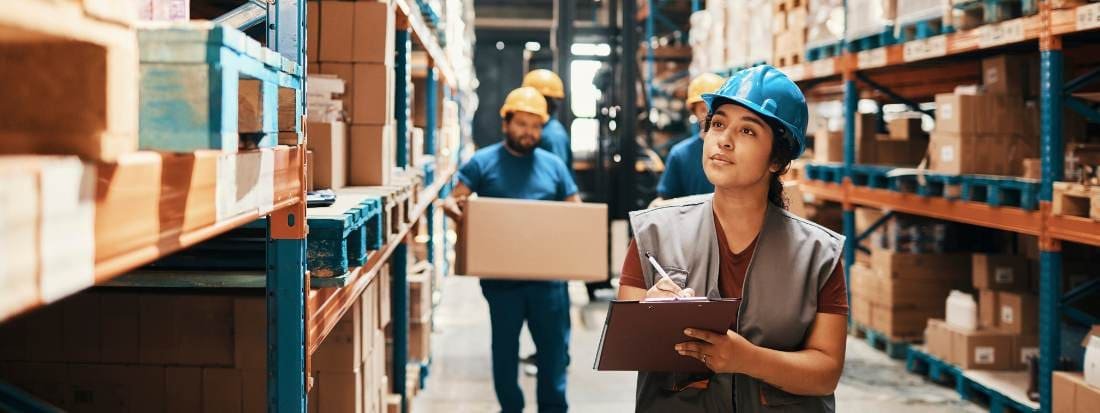
Enhance Warehouse Security Measures
Inventory shrinkage due to theft significantly impacts accuracy. Implement robust security measures such as controlled access points, surveillance cameras (CCTV), adequate lighting, background checks for employees handling high-value goods, and clear policies regarding inventory handling and removal.
Utilize Professional Storage and Handling Practices
Disorganization and improper handling lead to lost, damaged, or misplaced inventory. Ensure clear labeling (barcodes, RFID tags,…), logical warehouse layout, designated storage locations for each SKU, proper use of material handling equipment, and standardized procedures for receiving, putaway, and picking to minimize errors and damage.
Partner with Expert Fulfillment Providers like Keys Logistics
Collaborating with expert fulfillment providers like Keys Logistics significantly boosts operational reliability. Keys Logistics offers specialized cross-border services with self-operated warehouses in the US, UK, and Europe, adeptly handling fulfillment for platforms like Amazon, TikTok, and independent stores. They utilize advanced WMS, TMS, and integration technologies to ensure high accuracy and efficiency across millions of annual orders.
This partnership helps reduce operational costs and enhance customer satisfaction through streamlined processes. Their strategic global presence and comprehensive solutions, including returns management, offer scalable support for e-commerce growth. Entrusting fulfillment to experts like Keys ensures seamless operations.
Upgrade to Robust Inventory Management Systems
Manual tracking or basic spreadsheets are inadequate for complex operations. Invest in a capable Warehouse Management System (WMS) or inventory management software that offers real-time tracking, barcode/RFID scanning capabilities, integration with sales channels, and robust reporting features. Technology automates data capture and reduces human error significantly.
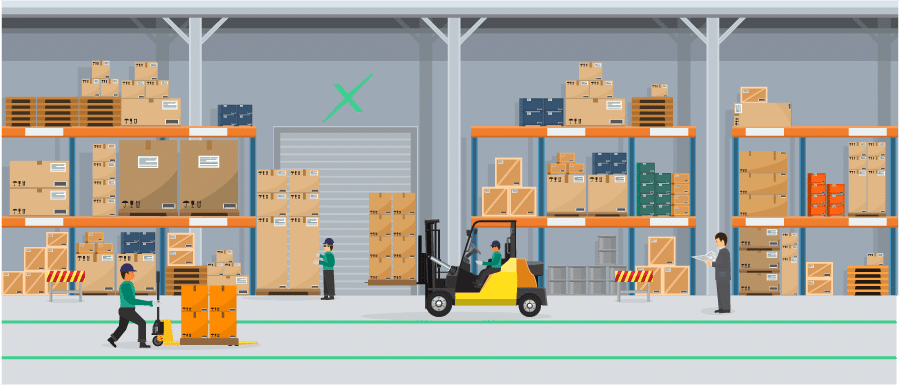
Perform Frequent and Random Inventory Audits
In addition to scheduled cycle counts, conduct unannounced spot checks or random audits on specific SKUs, locations, or processes. This helps verify the effectiveness of your regular counting programs and keeps staff vigilant about maintaining accuracy.
Inventory Accuracy FAQs
What Are the Common Causes of Inventory Inaccuracy?
Several factors contribute to discrepancies between recorded and physical inventory. Common causes include:
- Human error: Mistakes during manual data entry, receiving, putaway, picking, packing, or counting.
- Inventory shrinkage: Loss due to theft (internal or external), damage during handling or storage, or product spoilage/obsolescence.
- Receiving errors: Incorrect quantities recorded upon arrival from suppliers.
- Misplaced inventory: Items stored in the wrong location within the warehouse.
- Shipping errors: Sending incorrect items or quantities to customers.
- Unrecorded Transactions: Failure to record returns, transfers between locations, or removal of damaged goods.
- System issues: Software glitches, integration problems between systems, or incorrect unit of measure conversions.
- Labeling problems: Damaged, incorrect, or missing barcodes or RFID tags.
How Is Inventory Accuracy Percentage Calculated?
As mentioned earlier, the standard formula compares physical counts to system records:
Inventory Accuracy Rate (%) = (Number of Items Physically Counted/Number of Items on Record) x 100.
Alternatively, it can be calculated based on the value of inventory or the number of SKUs with accurate counts versus the total SKUs checked. The key is consistency in the chosen method for tracking progress.
What Is the Average Industry Benchmark?
While perfect 100% inventory accuracy is the ideal goal, it’s rarely attainable in practice, especially in high-volume operations. Industry benchmarks vary, but best-in-class companies often aim for and achieve inventory accuracy rates of 98% or higher. Some sources cite average rates closer to 95-97% for well-managed operations, while less optimized warehouses might fall significantly lower, sometimes even below 70% as noted by some studies.
The specific target should depend on the industry, product value, and operational complexity, but consistently striving for improvement towards the high 90s is crucial for efficiency and profitability. Maintaining high inventory accuracy is a continuous effort.
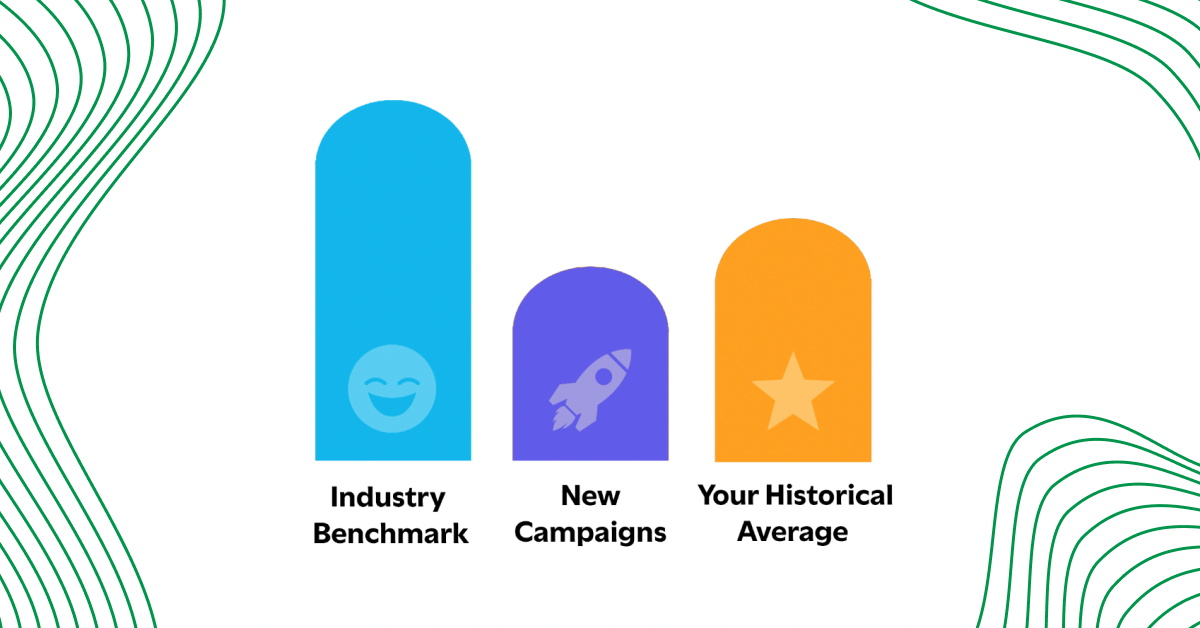
In conclusion, achieving and sustaining high inventory accuracy is fundamental to operational excellence in the demanding field of logistics. It transcends simple record-keeping, directly influencing customer satisfaction, cost control, financial health, and overall supply chain efficiency. By implementing robust processes like cycle counting, leveraging technologies such as WMS and real-time tracking, and fostering a culture of diligence, businesses can significantly reduce discrepancies. Ultimately, reliable inventory data empowers smarter decision-making and builds a resilient foundation for navigating the complexities of modern commerce and achieving a distinct competitive advantage.